ANALYSIS OF THE COLOUR REPRODUCTION
THROUGH DIFFERENT OFFSET PLATEMAKING SYSTEMS
Mahovic, S.; Agic, D. & Gojo, M.
Abstract:
"Computer to Plate" (CtP) technology has developed in the last ten years and it is today the subject of investigations of a series of manufacturers. Their aim is the same – the discovery of the most suitable copying layer on the printing forms, the development of the printing forms without processing, the usage of the most suitable energy source and the most suitable output devices geometry. On the graphic product market, there are considerable number of the producers of the output devices and the printing plates, but their products have not yet been standardized. Only a few of them are compatible with each other, and the two basic technologies have been defined: the thermal technology and the “visible laser” one.
In this work, the most represented CtP technologies of the world known manufacturers have been investigated and compared with the conventional production process of the printing plates. The investigations we made are of significance in the field of graphic reproduction. It defines the advantages and the disadvantages of the each observed technology. The analysis of the investigation results determines the differences in the print quality obtained by the usage of the observed technologies by measuring the relevant parameters for monitoring the reproduction.
Key words: conventional and CtP platemaking systems, offset printing, print quality
1. Introduction
The incursion of the technical revolution into all the areas of the communication industry pushed the traditional reproduction processes into the history. The boundaries among the prepress departments, photographic laboratories, photographs processing and printing departments disappear gradually. The simultaneous development of the devices, computer systems and program applications influenced numerous novelties in the processes of the graphic industry. The tendency is to produce smaller devices and to eliminate the greatest possible number of intermediate processors as well as the human factor, an important problem in the need of the production standardization. As the majority of the apparently revolutionary developments, "Computer to Plate" (CtP) technology is the product and the result of the investigations in several different fields. The spreading of the usage of the printing plates, laser technology, photopolymer chemistry and DTP influenced the creating of the existing CtP systems. The wish for quicker, cheaper and more qualitative production has forced the graphic firms to constant monitoring the market trends which causes and stimulates the further development of the same area.
The conventional process “Computer to Film to Plate” ( CtFtP) enables the production of the printing plates in a way which is mostly used today. From the computer, by means of the imagesetter the four films of the primary colours of the subtractive synthesis have been obtained (Cyan, Magenta, Yellow and Black). After the developing, the films are mounted by hand and copied on the printing plates. After exposing and processing the printing plate, its surface gets characteristic physical-chemical properties. Some surface parts are of hydrophilic character and in the reproduction process they attract water. Some parts of the surface are of oleophillic character and they attract ink. Thanks to the mentioned properties the surface of the printing plate enables the information transfer from the film onto the printing substrate by means of the determined ink. By using the CtP system for the platemaking, the printing plates have been produced directly from the computer by means of the platesetter. The surface of the CtP printing plate has the same physical-chemical properties as the conventional printing plate. There are series of digital printing plates on the market with different composition of the copying layers, the carriers of the printing surfaces in printing. By eliminating the phase of the film production, the time necessary for the platemaking is decreased and the possibility of the error appearance (deformations) decreases, which appear during the conventional platemaking process (e.g. in size and shape of the printing elements on the printing plates) (Agic et al., 1999). Because of that it was supposed that the usage of the different production processes of the printing plate would cause the appearance of the different deformations of the screen elements on the reproductions in spite of the same conditions of their realization (in regard to the printing substrate, ink, damping fluid and printing process). For investigation of such possible deformations the original has been defined which has been reproduced with the different platemaking systems and which has been printed in offset. The aim is to define the boundaries of the possibilities of the optimal reproduction in regard to the observed systems (the conventional system and the CtP one) in the same conditions of realization.
2. Background
Surely the most spread technique of planographic printing today is based on the transition of the printing ink from the printing plate on the transfer cylinder, which transfers the information on the printing substrate by means of the printing ink. The main representative of the planographic reproduction is the offset printing. The information transfer from the printing plate enables the characteristic relation of the non-printing areas and the printing elements, which are on relative the same level (Ihme, 1982). Thanks to different physical-chemical properties of the mentioned surfaces, the non-printing areas are referred to as the hydrophilic ones and the printing areas are hydrophobic ones. Because of that, the fountain solution (water with additives) will adhere only to the non-printing, hydrophilic areas and the printing ink will adhere to the printing, hydrophobic areas during the printing process.
2.1 Digital prepress
Today's digitalisation of the prepress enables simple input and processing of data, and great speed of the information transfer. It enables the preparation of one document as well as the whole sheet in form of digital record. The computer does the drawings, digitalisation, information screening, paging, copying and visual justifying of the whole page. It means, that digital format, ready for further reproduction, is formed from the pictures, texts and illustrations by the defined methods and procedures (Fig. 1)
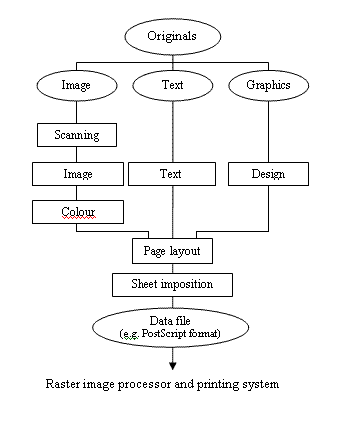
Fig. 1. Digital composition of a printed page (Kipphan, 2001)
The final view of a page is formed by integration of the picture and text as well as by shaping the graphically formed whole. The result of the mentioned prepress is the printing sheet, which contains the formed single colour and multicolour pictures and texts presented as the digital record. During the transfer and processing of digital data, three different printing processes aided by computer are differentiated: Computer to Film, Computer to Plate, and Computer to Press.
The conventional system of the information reproduction in graphic technology is based on the imaging processes and film processing which are copied on the printing plate. The obtained printing plate is processed depending on the technique of the reproduction realisation (e.g. offset). Thanks to the systems of the digital processing of data and automatic processing of films, great number of intermediate processes, which were unavoidable during the hand processing of films, are eliminated. Such automation of the prepress shortened the time of the past preparation for printing. It also influenced the decrease of the possibility of the error appearance in these intermediate processes. The further progress in the graphic industry is elimination of the film processing and the production of the printing plates directly from the computer. The devices for making records on the printing plates, the sources of great energy emanation and the characteristically coated printing plates are used for such technology and systems. By eliminating the processes of film imaging and developing, the total preparation time is shortened, the possible errors in the intermediate processes are avoided and the total costs of the reproduction material and production are decreased (Fig.2). By introduction of CtP technology not only the picture of the prepress department is changed but also the picture of the whole production.
Fig. 2. Conventional ( A ) and CtP ( B ) workflow
3. Printing platemaking systems
3.1 Conventional Computer to Film systems
Conventional system of the printing plate production comprises the application of the photomechanical copying processes from the original onto the printing plate. In the second half of the 20 th century the processes of the copying of originals (films) were in the middle of attention and development of the graphic industry. The films started to be used the reproduction of the colour separation, production of the proofs as well as the group of elements on the printing sheet necessary for the production of the printing plates. Except the mentioned, the film proved to be the ideal medium for long lasting information storage. It became the integral part of each graphic setting. Today it is gradually replaced by the direct production of the printing plates from the computers.
In the conventional system of the reproduction realization, copying is a very important process. While copying, the non exposed printing plate with the copying layer is exposed through the corresponding original, during which exposure the photochemical reaction appears on the exposed parts of the copying layer under the action of light. The copying layer is removed from the surface of the printing plate during processing and the remaining surface of the aluminum oxide presents the non-printing areas during printing. Copying layer remaining on the surface presents the printing areas (attracts ink) and enables the coloured printing on the corresponding printing substrate (Fig.3).
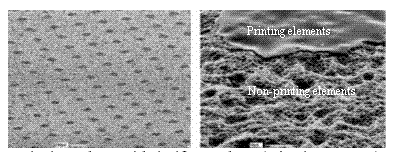
Fig. 3. Aluminum printing plate with halftone dots (Kipphan, 2001)
3.2 Computer to Plate systems
By commercial usage of CtP printing plates the researches in the field of graphic industry go in the direction of better and more qualitative development of that area and the application of the printing plates based on water in order to better protect the environment (Adams & Romano, 1996). Because of different kinds of the copying layers, and contrary to the conventional printing plates, the CtP printing plates can be exposed from the new sources of illumination, whose advantages were used by the manufacturers of CtP plates. Because of these advantages the CtP printing plates and systems can be divided in two main groups:
• “photo-mode” systems – laser beams cause photographic reaction in the active and photosensitive copying layer. Latent image appears in the copying layer which gives the final image on the surface of the printing plate during processing. Printing plates based on the silver halide by aluminum substrate are included in the “photomode” systems. Because the printing plates based on silver halide have been investigated in this work, the surface of such printing plate is presented in figure 4.
• “heat-mode” systems – copying layer is made from the material sensitive on infra-red light. Latent image appears by the action of the thermal energy in the active layer of the printing plate, which by processing gives the desired image on the printing plate. “Heat-mode” systems are made of the thermal printing plates (Van hunsel et al., 1998). The activity of the laser beams on the copying layer of the CtP printing plate will influence the different shape and characteristics of the printing elements on CtP thermal printing plates from the printing elements on CtP printing plates sensible to the visible part of the spectrum. The printing elements on thermal printing plates have characteristic shape with sharp edges and small unhomogeneousness (Fig. 5).
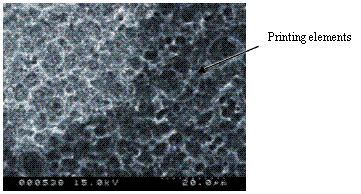
Fig. 4. Microscopic presentation of the silver halide printing plate
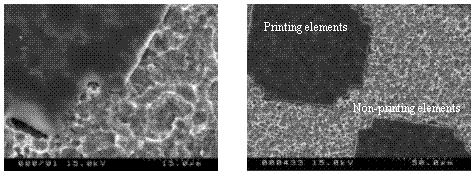
Fig. 5. Microscopic presentation of the thermal printing plate's surface
Characteristic shapes of the printing elements which compose the printing surfaces on the printing plates cause different plates of the screen elements on the prints. It was supposed that such characteristic shapes of the screen elements would cause the differences in quality of prints as well as the different curves of the tone reproduction.
4. Exprimental part
The foreseen investigations were based upon the fact that the conventional platemaking process prevails today in graphic industry. Independent from the choice and from the integrated platemaking system (CtFtP or CtP), the aim of each reproduction process is the same – obtaining the reproduction true to original. Because the different platemaking processes can influence the variety of the printing elements on the printing plates (Mahovic et al., 2003), the purpose of this investigation was the observing of these eventual differences and the defining of their influence on the quality of the prints.
The original with all the necessary measuring fields and the motives with the characteristic dominating tones for visual evaluation of the prints were reproduced. The original was reproduced in two different ways: by using the conventional platemaking process and the by the application of three different CtP digital platemaking processes. The possible changes in dimensions and plates of the printing elements on the printing plates, from the place defined on the original, and the appearance of the obtained deformations on the realized reproductions were assumed during the production of the printing plates by different processes.
In the conventional system, the printing plates with the diazo copying layers (on diagrams with the marks “1”) were used. From the CtP systems, the CtP device with the internal drum, violet laser and the silver halogenide copying layer (the mark “2”), the CtP device with the internal drum, IR laser and thermal printing plates (mark “3”) and the CtP device with the external drum, IR laser and thermal printing plates (mark “4”) were used. The spectrophotometric measurements were done on the samples. The obtained spectral data have been transferred into LAB values and the lightness, hue, saturation and colour difference of the observed prints have been defined (Wiszecky & Stiles, 1982).
5. Results
Because the colours differ in two directions (lightness and saturation) the parallel monitoring of both parameters is most often performed to get the more precise investigation results (Hunt, 1991). The measurements were performed on the full tone patches of the primary colours (cyan, magenta, yellow) and on the full tone patches of the secondary colours (red, green blue) of the subtractive synthesis. From the measuring results of lightness, it is visible that it decreases on each observed sample in regard to the original (Fig. 6). Only on the prints with CtP system (3) there is the considerable increase.
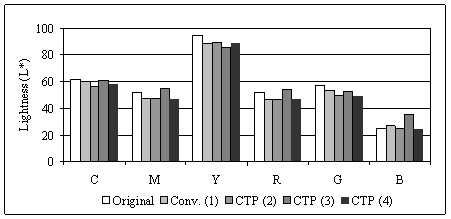
Fig. 6. Measuring results of lightness on samples.
Colour saturation results point at the increase in value for all colours and systems (except cyan and yellow) (Fig. 7).
Because of more precise colour description the hue angle has been defined as the attribute for defining the difference between the two colours. By the determination of the hue angle on the samples, the decrease on all the colours is visible (Fig. 8). Only in cyan the hue is uniform for all the observed systems; magenta is evidently decreased and there is the increase of the hue angle in blue.
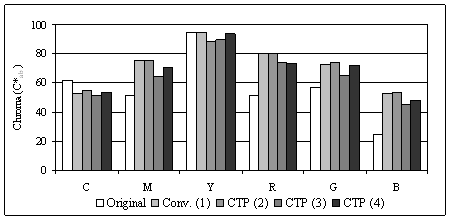
Fig. 7. Measuring results of chroma on samples.
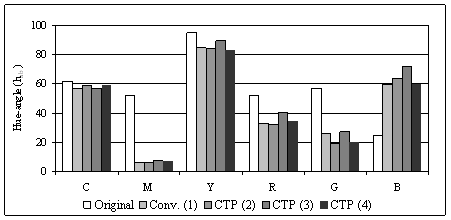
Fig. 8. Measuring results of hue-angle on samples.
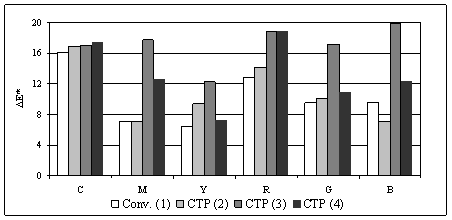
Fig. 9. Measuring results of colour difference on samples.
The colorimetric difference was also determined for the observed systems (Fig. 9). Colorimetric difference is the distance among the points of different colours defined in some colour space. This value gets the importance in the perceptional linear colour spaces such as CIELAB. According to the measuring results, in regard to the original, considerable aberration of all the systems is visible. The smallest aberration has the conventional reproduction system (1) and the greatest one has the CtP system (3) in all colours.
6. Discussion
The quality of reproduction can be influenced by a series of parameters such as the system of input units, printing process, conditions of reproduction, kinds inks and damping fluids, printing substrate, separation parameters and similar. The mentioned parameters in this work were strictly defined and it was believed that the conditions for reproduction were standardized for all the observed systems. The variations were done in the intermediate process i.e. in the process of platemaking. Because of that the investigated parameters could point at the quality of the print reproduction in regard to the application of a particular system for platemaking.
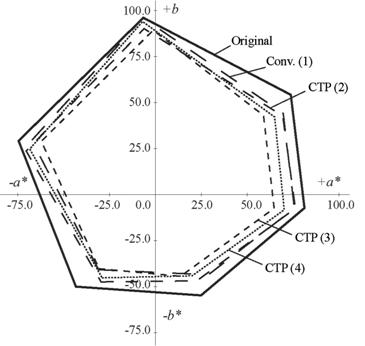
Fig. 10. Colour gamut in CIEL*a*b*diagram.
Lightness, saturation and hue angle are some of the relevant characteristics for the reproduction quality monitoring. It is visible from the observed diagrams that defined changes appear on all prints in the sense of decreasing the measured values. Such investigation results have shown to be identical in presenting gamut in CIE LAB colour system (Fig. 10). The values a* and b*, determined by measuring the prints, are evidently smaller than the values on the original, for the observed reproduction systems. In this way the range of colour reproduction in all the reproduction systems is decreased, most on the prints realized in CtP system (3).
7. Conclusions
The integration of the new digital technologies demands the settling in and adaptation of the whole reproduction process. The conventional reproduction system has been used for years and the need for the production adaptation has developed to the level which enables the obtaining of high quality prints. The application of the CtP processes in platemaking accelerates the reproduction process, but the adaptation of the reproduction process has not been completely solved. This can be concluded from the measuring results where the lightness, saturation, hue and the colorimetric difference differ in all the observed systems in regard to the original but the values of the difference of the conventional print are the smallest ones.
In visual observation of the reproductions with the characteristic prevailing tones, the results were uniform. The conventional system for platemaking has optimally reproduced the motives with the prevailing light and dark tones, shadows and details. In CtP systems, the results of the visual evaluation were not uniform. CtP system marked by (3) has been stressed, where the light tones and the details on prints were lost, as well as the shades on the dark motives. Because the digital platemaking process gives more regular form of the printing elements (Mahovic et al., 2003) simpler standardization of the production in the digital surroundings is evident.
For reproduction standardization the application of the Colour Management is suggested, which will ensure the optimal reproduction in regard to the used input and output reproduction devices and in regard to the used materials in the production.
8. References
Adams Richard, M. & Romano, F. (1996). Computer to Plate: Automating the PrintingIndustry , Graphic Arts Technical Foundation , USA
Agic, D.; Mandic, L. & Gojo, M. (1999). Influence of Some Parameters on the Change of Printing Elements Dimension, Proceedings of 10 th International Daaam Symposium, Katalinic, B., pp. 5-6, ISBN 3-901509-10-0, Vienna, October 1999, DAAAM International Vienna, Austria
Hunt, R. W. G. (1991). Measuring Colour , Ellis Horwood Limited, ISBN 0-13-567686-X, England
Ihme, R. (1982). Lerhbuch der Reproduktionstechnik, VEB Fachbuchverlag, Leipzig
Kipphan, H. (2001). Handbook of Print Media, Springer, ISBN 3-540-67326-1, Berlin
Mahovic, S.; Agic, D. & Gojo, M. (2003). Mechanical and Optical Differences in Long Run Printing in Conventional and CtP Offset Systems, Proceedings of IARIGAI, Lovrecek, M. (Ed.), pp. 213-221, ISBN 953-96276-8-0, Dubrovnik-Cavtat, September 2003, Acta Graphica Publishers, Croatia
Mahovic, S.; Mandic, L.; Agic, D. & Gojo, M. (2003). Optical Comparison of Reproduction in the Closed Graphic Systems, Proceedings of 14 th International Daaam Symposium, Katalinic, B., pp. 281-282, ISBN 3-901509-34-8, Sarajevo, October 2003, DAAAM International Vienna, BiH
Van hunsel, J., Van Damme, M., Vermeersch, J. & Elsässer, A. (1998). Thermostar: A new Thermal Litho Printing Plate Technology for CtP Recording, TAGA Proceedings, pp. 395-409. Rochester (NY)
Wyszecki, G. & Stiles, W.S. (1982). Color Science: Concepts and Methods, Quantitative Data and Formulae-2nd Edition, John Wiley & Sons, ISBN 0-471-02106-7, Canada