The 16th INTERNATIONAL DAAAM SYMPOSIUM
"Intelligent Manufacturing & Automation: Focus on Young Researchers and Scientists" 19-22nd October 2005
IMPLEMENTATION OF SIMULATIVE METHODS INTO PRINTING PROCESS
Njezic, Z.; Ziljak, V. & Babic, D.
Abstract:
The method for simulation of printing flows provides new proposals for improvement, upgrading, management and planning of graphic processes in the area of graphic
engineering. Applying the simulation of whole production flow, extremely risky situations can be identified and maximum production possibilities of the system can be defined. Simulation of work of relevant components in the production process points to precise determination of bottle necks as well as congestions in the production flow. Based on the measurements and the analysis of the received results, more optimal and adjustable settings of the production parameters in the graphic production have been created. Thereby, the modelling of graphic system has been introduced as successful method for production enhancement and production optimisation. There has been obtained a new observation and evaluation approach for graphic production flows, from preparation until final flows. Finally, this is reflected by production growth, stable production line and enhanced utilization of existing digital equipment.
Key words: simulations, printing, estimation, normative provisions
1. INTRODUCTION
The paper contains model designs for simulating the work of a prepress, printing and final processing production plant. Virtual production units have been made with all the necessary parameters, and activities comprising separate production segments are additionally described. Real characteristics and measured time units of printing machines in the graphic production process have been built into the virtual machines (Njezic et al., 2003). Thus the list of the machine sequence was obtained in respect to cost-efficiency, related to certain types of jobs and the compensation in respect to the integral system of determining the digital job order (Ziljak et al., 2004). With the help of simulation results were obtained that improve and raise the process of production control and planning to a higher level and enable additional JDF embedding (Ziljak & Koren 2003). The goal was to build as many as possible real production situation models; to archive the obtained results into databases, thus aiming at making thorough computer science descriptions of graphic production units and situations, with the goal being to develop standardization in the printing business production.
2. SIMULATION METHOD IN PRINTING PRODUCTION
With the help of the method where graphic production flow is modelled and simulated, new proposals are given for enhancing, extending, control and planning of graphic processes in the graphic production cycle. By defining the graphic variables and by building models, a virtual printing plant is designed with all its belonging production elements. Simulation of certain printing phases aimed to find a stabile production plan and calculation lead to stochastic modelling (Njezic et al., 2002).The simulation method means simulating an enormous number of cases in order to be able to study many situations. Data generating is made from generator algorithms of random numbers, whereas the functions for generating random variables were obtained on basis of measurements made in real printing processes. Parameters taken here are the specific ones for a certain production phase (machine, colour, materials, human factor). In order to begin studying the production's weak points and set the standardization in production by using stochastic methods, it is necessary to gather the data on production elements in normal production conditions. By simulating the complete production flow, extremely risky situations are determined and the maximum production possibilities of the system are defined. With the help of production element operation simulation, efforts will be made to precisely determine production bottlenecks, and to create the optimum and best coordinated setting of graphic production parameters on basis of result measurements and analysis (Ziljak et al., 2003).Process flows have become open and complex, and each segment is labelled with the degree of probability and chance. Graphic system modelling is introduced as the successful method for production flow improving and optimization. The result following simulation is a new approach in respect to graphic production flow observation and evaluation, from the prepress stage to the final processing. On basis of experimental results, a rise in production is expected, the establishing of a more stabile production line and better use of the existing digital equipment, and the most important – opening of new work posts and occupations in the graphic production cycle. Modelling and simulation methods supplement the
uncoordinated situation of the entire graphic production line, with the goal being to design a system that will improve and develop a higher automation and informatics level .
3. DEFINING PRODUCTION NORMS
It is possible to improve graphic production processes with the help of digital standardization, modelling and simulation methods. Advancement, flexibility and capability to adapt to new solutions in the printing business are expected, as well as determining reasons for production delays, and what is most important, to make an impact in training personnel to work in production. It is possible to enter the very core of the printing system with the help of simulation methods and to describe it in
detail, and to improve considerably and develop the existing knowledge in the field. Designing of a new graphic product today unites several different technologies of production and this dictates a new approach to the product's making. A printing press's flexibility will result in making better-quality solutions for better competition. This new manner of understanding the market dictates implementing new modelling and simulation methods, including expert and consulting teams in quest of new solutions. As there is an indefinite number of solutions and an indefinite number of unpredictable situations, the best solutions are obtained when the simulation method is used on basis of predicted problems in a real-life system. Thus market demands are predicted on one hand, and a dynamic system is formed on the other hand that will produce new graphic products in a very short space of time. When prepress production was researched, classification was made into the following: graphic design comprising the factor of production and the style sheet criteria, make up with the same elements as the graphic editing, and scanning with determined coloring and size of the original.
4. EXPERIMENTAL TESTING
Models were designed that were used for continuous research of editions for a number of pages from 4 to 128 and so on (Fig.1.), regardless of the data in the concrete call for offers. Many variables are present in the description of the graphic product production including: printing machines for the given printing works, human resources, materials, time periods necessary for certain production phases, all in differently defined value scopes. The simulation was carried out for determined ranges in case of the prepress production part, with the belonging contents and demand criteria for individual pages.
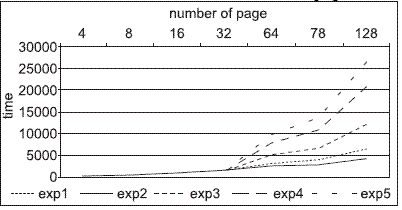
Fig. 1. Result of testing with simulation methods
A system describing individual graphic products is proposed for the prepress production standardization process. The description parameters define the graphic design, making up, scanning and specific accompanying jobs. Graphic design has been divided into the production factor and style sheet criteria. The graphic design production factor has been classified as: new (if the graphic design is being done anew), remodelled (if the graphic design has been changed) and repeated (if the
graphic design is repeated). In order to have better control over the graphic design, it is necessary to link the factor of the graphic design making with the graphic design style sheet criteria. The following classification has been proposed for the graphic design style sheet criteria: regular (for a style sheet produced in a regular way), medium (for a style sheet produced with medium difficulty), difficult (for a style sheet produced with difficulty), special (style sheet produced with great difficulty). A further breakdown in classification of the style sheet difficulty factor is possible, depending on what a certain graphic design firm specializes in. This paper will keep using the specified description for style sheet criteria. The graphic make up phase may also be divided into the production factor and style sheet criteria. The make up production factor is described with the make up elements: dummy (the dummy is the starting point), pre-dummy (the predummy is the starting point), 1st revision (the 1st revision is the starting point) and additional revision (the additional revision is the starting point). The making up production factor and the style sheet making up criteria are linked parameters in order to have a more complete covering of the making up phase estimate. The make up values for the style sheet making up criteria are: smooth1 (the most simple style sheet form, fastest in making), smooth 2, average1, average 2, average 3, special 1, special 2 (the most difficult style sheet form, slowest in making). The values between smooth 1 and special 2 are levels ranging from the most simple to the most complicated style sheets, and it is therefore also open for additional classification for individual production situations. The process of digitizing the original is linked with two factors – the category of scanning and the sample size A classification of three different records is given for the category of scanning: single shade of plain colour (for single shade originals), multi-shade plain colour (for multi-shade plain originals) and multi-shade multi-colour (for multi-shade multicolour originals). The sample size category is classified into four sub-categories, namely: minimum size up to A5 (size up to A5), medium size from A5 to A4 (sizes from A5 to A4 format) size over A4 (sizes over the A4 format), special requirements (formats that fall outside the set sizes).
5. CONCLUSION
The space for the possible initiators of simulation experimental printing processes starting up may be through a table of standards or mathematical relative algorithms. Simulating processes are based on real standards for individual printing presses. Making concrete estimates is vital for the administration of a printing business organization. Computers and new programs for estimating cost-efficiency production enable simulation of an enormous number of combinations and automatic search for what is better and for better situations. Finding new production paths for making an individual product is the goal of simulation as well as to get away from the
standard behaviour in making decisions for production paths. This type of approach makes way into the area of opening new work posts and planning of graphic production organization, as well as enhancing and bringing the total level of science and knowledge to a higher level. The purpose of simulation is evident in several large segments, namely: firstly in determining the optimum workflows immediately before printing start-up, secondly in determining the production bottlenecks, and thirdly - in investment planning, and fourthly - the simulators enable us to have the feeling of real physical printing press control and control of the postpress jobs without any material cost. Thus one gets closer to determining optimal ways in solving production problem situations, and remote control of production flows has been set.
6. REFERENCES
Njezic, Z.; Ziljak, V. & Pap, K. (2002). Design of Digital Graphic System, Proceedings of the Design 2002, Marjanovic, D. (Ed.) 867-872, Faculty of Mechanical Engineering and Naval Architecture & The Design Society, ISBN 953-6313-47-9, Zagreb
Njezic, Z.; Ziljak, V.; Pap, K. & Svilicic, B. (2003). The stochastic model of simulation of a virtual printing-house, Advances in printing Science and Technology, Lovrecek, M. (Ed.), 163-171, Acta Graphica Publishers, ISBN 953-9676-8-0, Zagreb
Ziljak, V.; Pap, K.; Njezic, Z.; & Ziljak, I. (2004). Printing process simulation based on data for standards taken from actual production, Advances in printing Science and Technology, Lovrecek, M. (Ed.), 237-244, Acta Graphica Publishers, ISBN 953-96276-9-9, Zagreb
Ziljak, V.; Pap, K. & Simovic, V. (2003). The simulation of integrated conventional and digital entrepreneurship system models with the financial parameters, 15th International Conference on Systems Research, Informatics, and Cybernetics- INTERSYMP - best paper award, ISBN 953-99326-0-2, Baden-Baden
Ziljak, V. & Koren, A. (2003), Modelling and Simulation as a Planning Method for Printing Houses Modernitazation with JDF, Available from: http://www.ziljak.hr/vilko/VZbiografija/Foi%20VZ%20AK%20clanak%20simulacija%20JDF.doc Accessed: 2005-05-15